JHF Helps Reduce Scrap, Rework, and Safety Concerns with Custom Assembly Table
Posted by Admin
Background:
JHF’s customer assembles an awkwardly shaped plastic product for their key customer. To achieve the required torque during installation, they were using a high-speed rundown tool for rough assembly and a manual torque wrench for the final tightening. This resulted in final product quality issues- If the final torque was too low, the product would leak- resulting in rework… too high, and the threads would deform, causing the product to be scrapped at their expense. Multiple operators were needed to complete this awkward and repetitive process, posing a safety concern.
Solution:
JHF sent in our assembly tool specialist. He used a precision assembly system at the customer’s facility to determine the ideal requirements for the job. JHF’s engineering and fabrication teams then designed and built a turn-key, ergonomic assembly workstation with an integrated Ingersoll Rand DC electric fastening system and a modular work holding cradle.
Impact:
Cycle time was reduced and rework and scrap decreased dramatically. With the use of the DC tool system- which provides torque values with repeatability of 1-3%, they can perform ergonomically safe assembly with only one operator- freeing up resources and machinery (including the modular cradle) for other tasks and preventing injury. They are also able to provide recorded torque data to their customer for long term quality assurance.
Call JHF- St. Louis, today, for custom solutions to your application challenges. 1-800-444-0522
Or
Contact your local representative, today.
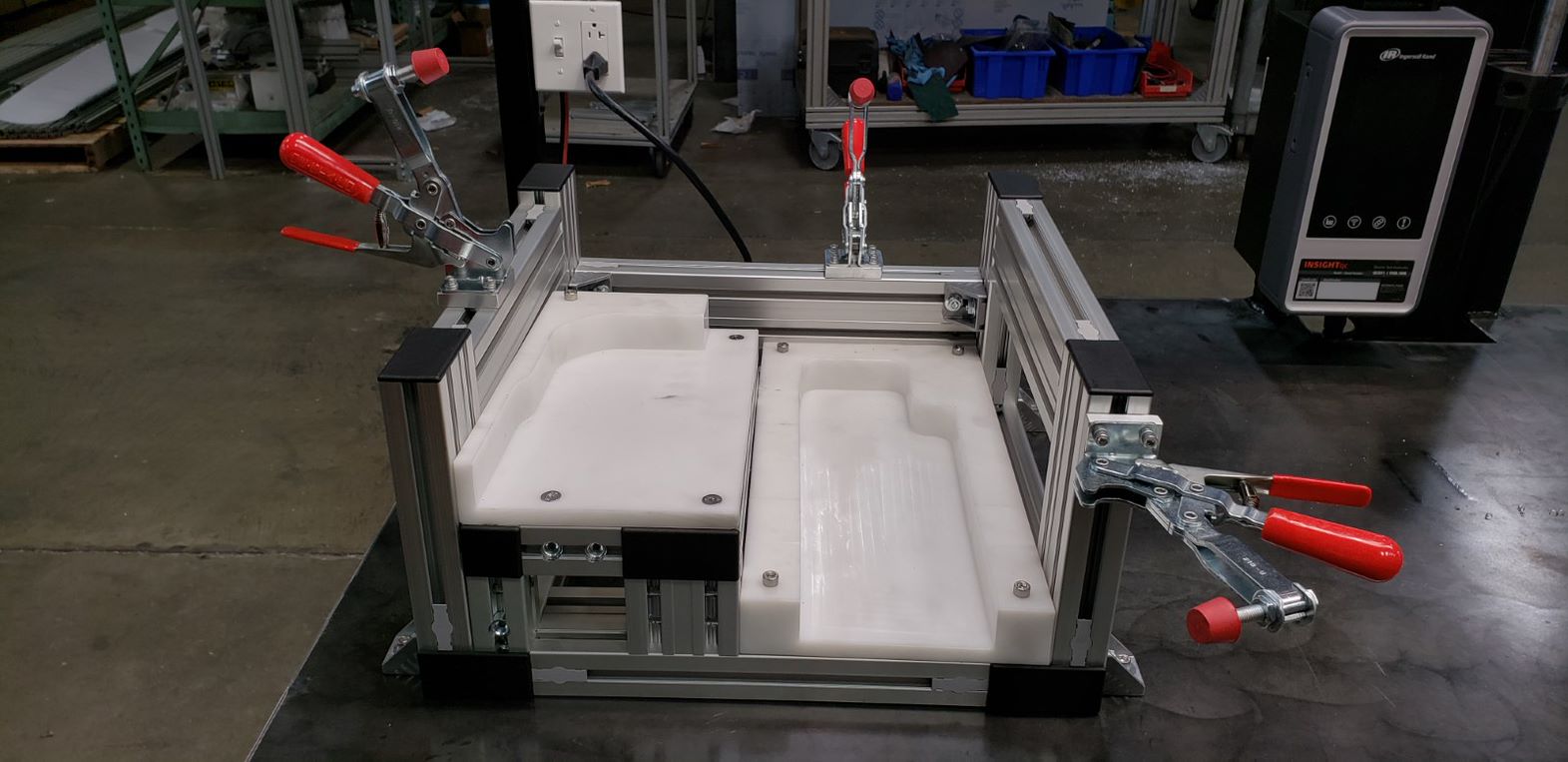
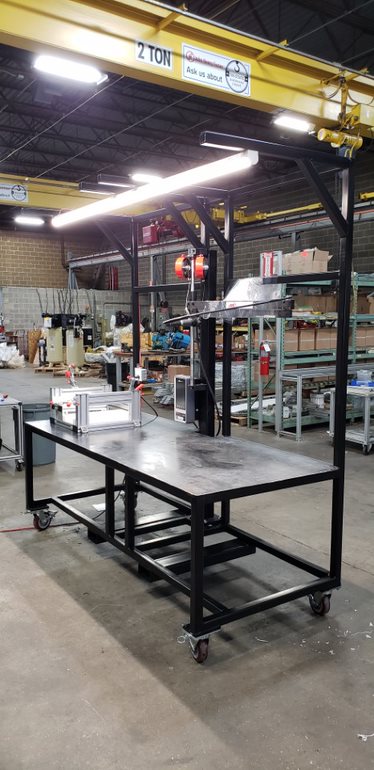
Call JHF- St. Louis, today, for custom solutions to your application challenges. 1-800-444-0522
Or
Contact your local representative, today.